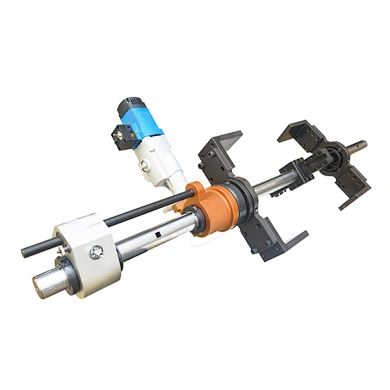
# Flange Facing Machine: Essential Equipment for Precision Surface Finishing
## Introduction to Flange Facing Machines
Flange facing machines are specialized tools designed to create precise, smooth finishes on flange surfaces. These machines play a crucial role in various industries where proper flange sealing is essential for system integrity and safety.
## How Flange Facing Machines Work
Flange facing machines operate by rotating cutting tools across the surface of a flange while maintaining precise control over depth and angle. The process typically involves:
– Mounting the machine securely to the flange
– Adjusting cutting parameters based on material and finish requirements
– Executing controlled passes across the surface
– Verifying surface quality with precision measuring tools
## Key Applications of Flange Facing Machines
These versatile machines find applications across multiple industries:
– Oil and gas pipeline systems
– Power generation plants
– Chemical processing facilities
– Shipbuilding and marine applications
– Heavy industrial equipment maintenance
## Advantages of Using Flange Facing Machines
Keyword: Flange facing machine
Modern flange facing equipment offers numerous benefits:
– On-site machining capability eliminates flange removal
– Precision surface finishes ensure proper gasket sealing
– Reduced downtime compared to traditional methods
– Cost-effective alternative to flange replacement
– Improved safety by maintaining system integrity
## Choosing the Right Flange Facing Machine
When selecting a flange facing machine, consider these factors:
– Flange size and material specifications
– Required surface finish quality
– Portability needs for field work
– Power source availability
– Budget constraints and ROI considerations
## Maintenance and Safety Considerations
Proper maintenance ensures optimal performance:
– Regular cleaning of cutting tools and machine components
– Lubrication of moving parts as specified by manufacturer
– Inspection of electrical components (for powered models)
– Proper storage when not in use
– Following all safety protocols during operation
## The Future of Flange Facing Technology
Advancements in flange facing technology include:
– Automated control systems for improved precision
– Integration with digital measurement tools
– Lightweight materials for enhanced portability
– Smart monitoring systems for predictive maintenance
– Environmentally friendly machining processes
Flange facing machines continue to evolve as essential tools for maintaining critical infrastructure across industries worldwide.