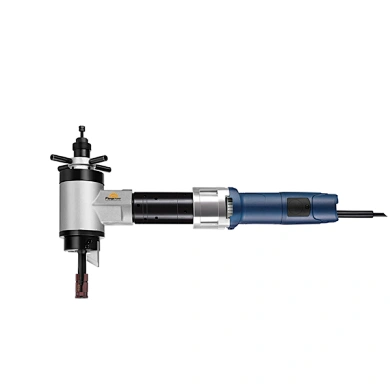
# Flange Facing Machine: Essential Tool for Precision Flange Machining
## What is a Flange Facing Machine?
A flange facing machine is a specialized piece of equipment designed for machining and resurfacing flange faces with high precision. These portable machines are essential in various industries where flanges need to be prepared or repaired without removing the pipe from its installed position.
## Key Features of Modern Flange Facing Machines
Modern flange facing machines offer several important features:
– Portability for on-site machining operations
Keyword: Flange facing machine
– High precision cutting capabilities
– Adjustable cutting speeds
– Compatibility with various flange sizes
– Durable construction for industrial environments
## Applications Across Industries
Flange facing machines serve critical functions in multiple sectors:
### Oil and Gas Industry
In pipeline systems where flange surfaces must maintain perfect sealing integrity
### Power Generation Plants
For maintaining steam and water system flanges in turbines and boilers
### Chemical Processing Facilities
Where corrosive environments demand frequent flange maintenance
### Shipbuilding and Repair
For maintaining flange connections in marine piping systems
## Advantages Over Traditional Methods
Using a dedicated flange facing machine provides significant benefits compared to conventional machining approaches:
– Reduced downtime as pipes don’t need disassembly
– Cost savings from avoiding complete pipe removal
– Higher precision results than manual methods
– Improved safety by minimizing handling of heavy components
– Consistent quality across multiple flange surfaces
## Maintenance and Operation Tips
To ensure optimal performance from your flange facing machine:
– Regularly inspect cutting tools for wear
– Keep all moving parts properly lubricated
– Follow manufacturer’s guidelines for speed settings
– Use appropriate clamping force for stability
– Clean the machine after each use to prevent buildup
## Choosing the Right Machine
When selecting a flange facing machine, consider:
– The range of flange sizes you need to work with
– Available power sources at your work sites
– Required precision levels for your applications
– Portability needs for your specific work environment
– Available accessories and tooling options
## Future Developments
The flange facing machine market continues to evolve with:
– Increased automation features
– Improved material compatibility
– Enhanced digital controls
– Lighter yet more durable designs
– Better integration with measurement systems
For professionals working with piping systems, investing in a quality flange facing machine can significantly improve efficiency, reduce costs, and ensure the highest quality flange surfaces for critical connections.